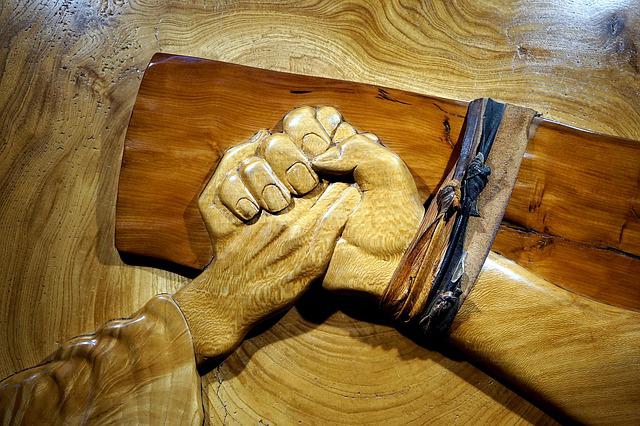
First, choose a piece and then make the required cuts to carve a face in wood. Using a step-by-step video, follow along as the expert guides you through the process. The progressing cut will make carving the face much more realistic. A lifelike face can be created by the progression of the noses on the wooden piece. To give your face a more realistic look, you can also use shellac and colored dyes.
Hardwoods
You must consider the type and size of the wood that you are using before carving a face. Hardwoods can be described as a group of trees with large leaves that can thrive in many climate zones. They are suitable for many purposes including furniture and building because of their high density, strength and beautiful appearance. Although hardwoods are less expensive than softwoods, they can also be strong and resistant to fire.
You might want to try wood carving if you are new to the art. These types of wood are easier to work with and are a good choice for beginners. However, you should remember that softer woods cannot hold the same quality and finish as hardwoods. Try different types of wood before you settle for one.
Softwoods
The first step to carving a face in wood involves choosing the softwood. Softwoods are often more difficult to carve and have more knots. They are also more likely to crack if you use big strokes. The smallest pieces of wood will be cut by a beginner carver, which reduces the amount of detail. While it's not a major problem, this is something to be aware.
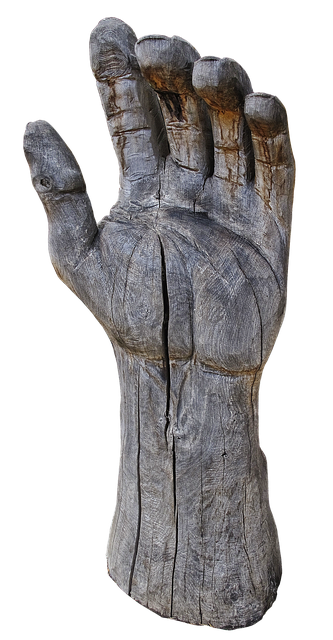
Some hardwoods are easier to work with than others. Aspen butternut, basswood and butternut are some of the easiest to work. It is recommended to use knives with a higher bevel. Softwoods are easier than hardwoods to work with, and can be carved along the grain or across it. The quality of your finished product will depend on the wood you choose for carving.
Colored Dyes
You can create a bright, detailed finish to a wood carving by using colored dyes. You can find these in a wide variety of colors and mix them with water or alcohol to create a unique colour. Colored dyes can be mixed with shellac for lighter woods. After applying dyes, ventilate your work area and clean your brushes with denatured alcohol. Paste wax is another option. Excessive glossiness can distract you from your work. Use 0000 steel wool to remove excess glossiness.
There are many types of wood dyes that can be used and they are easy to apply. Wood dyes will work with all topcoats. They are also easy to apply. They solve common finishing challenges. Because they come in a wide array of primary colors, they're easy to mix and apply. They come in many different shades, so you can mix them according to your personal preference. You can mix them to make unique colors.
Shellac
You should always have a jar of shellac handy before applying it to wood carvings. Shellac can be purchased in a jar, but it's easier to apply with a brush. A two-pound cut is sufficient. This is because the shellac will gradually build up and will reduce brush marks. Also, it's better to buy a thicker cut than a thinner one, because shellac is very water-thin. Make your own pad out of small pieces of cotton and lintfree cloth. This will ensure you get the right amount. Then, dip the tip of your brush into the shellac and let the excess flow back into the bottle.
Shellac can be used for accenting grain or adding color. Shellac comes in various colors, so you can create custom blends by mixing different shades of the resin. You can even darken the shade by applying extra coats of the lac. Shellac doesn't get cloudy or yellow like other wood finishes. It will also last longer, so you can make more faces. This is possible with any type of wood carving project.
Gouges

There are many types of gouges. The straight and palm types of gouges tend to be the most popular. Straight gouges are meant to be held by the hand while palm gouges use shorter shafts and more manageable handles. Hand held carving is easier with the shorter handles. These palm gouges can also be called veiners. They are perfect for carving faces into wood. Here are some tips before you start carving.
First, learn how to choose the best gouge. The gouge you choose should be able to carve a shallow v-shaped groove. A sharp edge and small sweep are essential features of a good gouge. Gouges are commonly classified by size. A 3/10 gouge will create the same-sized cut as an 5/10 gouge. As the first number increases, the scoop between the edges becomes deeper and the sweep gets progressively more curved. A gouge with a small stroke will create a shallow profile.
FAQ
How often should new supplies be purchased?
Over time, you may need to replace your tools. You'll need to sharpen your hand tools regularly if you use them. If you are using power tools, you will need to purchase replacement parts regularly. You can spread your purchases over a number of months to avoid spending too much.
What tools do I need to start as a woodworker and what should I learn?
Woodworking is an art. It requires patience. It takes time to master all the tools and techniques involved in woodworking.
There are many kinds of woodworking equipment currently on the marketplace. Some prefer to use power tools, while others prefer to use hand tools.
It's your choice. But you should ensure that you pick the right tool. If you don't have any experience, you may consider starting with a basic set of hand tools.
A router is a tool that cuts intricate shapes in wood. You can also learn how to use it. These can be found at most hardware shops.
How much should a hobbyist invest to get started?
A lot of capital is required to purchase the necessary supplies and tools if you want to start your own woodworking shop. The best place to start is by buying a small drill press, circularsaw, circular saw or sanding machine. These items don't cost much so they won't break your budget.
How can you calculate woodworking pricing?
It is crucial to keep project costs as low-cost as possible. Make sure you're getting the best prices on materials. You should also consider other factors that could impact the cost of your project, such as experience, skill level, time, and money. Our guide to the average household DIY task price will give you an idea of how much it costs to complete different types of woodwork projects.
How do I organize my shop?
The first step toward keeping your workshop clean and organized is to set aside a designated area for storing tools. To keep your tools sharp and ready for work, keep them clean of dust and debris. Hang tools and accessories using pegboard hooks.
What is the difference between a hobbyist or a professional woodworker, and how can you tell?
Hobbyists are passionate about making things from wood, while professionals tend to be more focused on the quality and craftsmanship of their work. Hobbyists take great pride in their creations, and share them with family and friends. Professionals will spend hours looking at designs before they start to build a project. They'll be meticulous about every aspect of their work, from choosing the best materials to finishing it perfectly.
Statistics
- The best-paid 10 percent make $76,000, while the lowest-paid 10 percent make $34,000. (zippia.com)
- Most woodworkers agree that lumber moisture needs to be under 10% for building furniture. (woodandshop.com)
- Woodworkers on the lower end of that spectrum, the bottom 10% to be exact, make roughly $24,000 a year, while the top 10% makes $108,000. (zippia.com)
- If your lumber isn't as dry as you would like when you purchase it (over 22% in Glen Huey's opinion…probably over 10-15% in my opinion), then it's a good idea to let it acclimate to your workshop for a couple of weeks. (woodandshop.com)
External Links
How To
Tips for driving a nail in wood
When driving a nail into wood, it is important to first choose the correct size and kind of hammer. The most common types of hammers are claw hammers, sledgehammers, mallets, ball peen hammers, and hatchets. Each type of hammer has its pros and cons. For example, a claw hammer works best when you want to hit something hard, like nails; however, it's difficult to control precisely where the blow lands. A sledgehammer allows you to hit large areas simultaneously, but it is too heavy and cumbersome to use for small tasks.
Place your hand flat on the side of your chosen hammer so that the handle rests in your palm. Hold the handle in your hand, but don’t force it too hard that you break. Keep your wrist relaxed and the hammer straight up. You should then swing the hammer straight up, keeping your wrist relaxed. You should feel the impact on the nail from the hammer. Try swinging a hammer using a block wood to practice until you are comfortable.
You can now drive the nail by holding the hammer to your body. You will need to position the nail so it is parallel to the wood. Keep your focus on the tip of each nail. Then, swing the hammer forward. Next, follow the motion of your hammerhead. Keep doing this until you are comfortable with the swing. Once you have mastered this technique, increase the power of your swings. You can hold the hammer over your shoulder and forcefully bring it down. This will allow you to exert more energy.
Once you've made the first nail hole, take out the hammer. To remove the remainder of the nails, you can use a screwdriver/pry bar. You should ensure that the nails are flush with the board's surface to avoid splitting the wood.