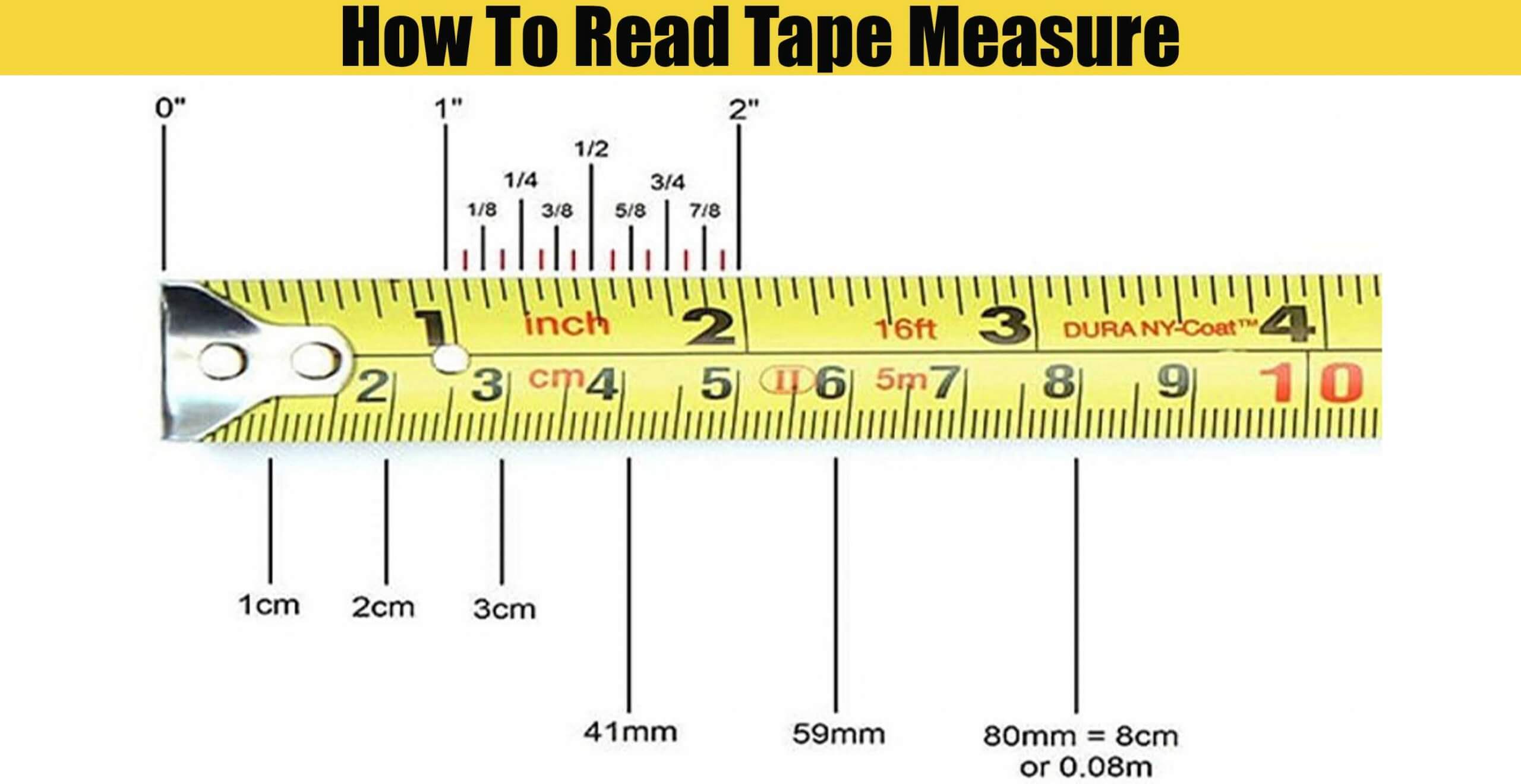
It can be challenging to transport rough lumber by hand. Be sure to take your hand saw and tape measure with you when you go to the store. Also, make sure to buy extra boards in the event that the one you have purchased doesn't fit. Make sure you have the right knots and checks on your board. Otherwise, they might not fit as well as you would like. You don't want a board that is too small and has to be cut up again. This will waste time and money, so it's best to buy one or two extra boards.
Minimal wastage
A sawmill turns roughly 59% of the rough lumber into boards. The rest of a log is usually waste: sawdust chips, bark and chips. Although a less perfect cut can result in more waste than a perfect cut, it should still not exceed 20%. Here's a simple formula to estimate the amount of wasted wood in a board. For a 4-foot board, the sawmill must remove 18% from its volume to obtain the desired lumber thickness.
For one thing, rough lumber rarely comes in uniform dimensions. The dimensions for hardwood bought at big box stores are often known so you can plan your project around that size. The rough edges of lumber can be uneven, which leads to wasted material. Additionally, rough-cut lumber often requires a common width which results in a lot wasted lumber. These wastes can't be recycled later.
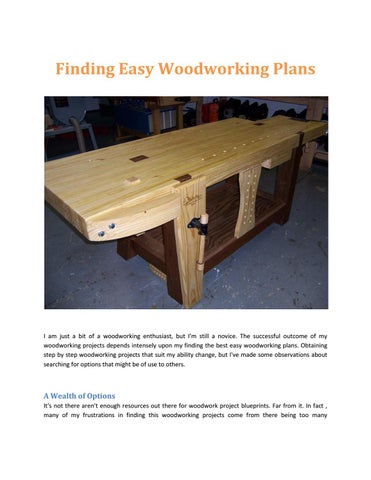
Preparation
Before you begin to cut rough lumber, measure its length. When rough lumber arrives at the lumber yard, it may not be flat. You may need to flatten it several times as it may not have parallel edges or faces. As a rule of thumb, you should remove 1/16 inch per pass. If the lumber has concave surfaces, run it through the saw with the concave surface down.
Rough cut lumber should be flattened to a thickness of 1/4 inch before it is cut. After flattening your face, plane the board to the desired thickness. Measure the length and width of the finished lumber once you have determined the thickness. You should account for any imperfections. You should leave about a quarter inch between the boards. Then, plan your project around the available boards. Hard to work with lumber that is too warped, bowed or twisted.
Cost
There are two types: rough-sawn and dimensional lumber. Home improvement stores usually carry finished lumber, but not often rough-sawn lumber. Both types are available in lumber yards and local sawmills. There is a difference in how much work it takes to process the two types. Because it takes less work to make, rough-sawn boards are more affordable. It is also thinner and wider than finished lumber.
Purchasing lumber from a mill or lumber yard is generally cheaper, but it is less likely to come in standard lengths. Making your own lumber can save you money over buying rough-sawn lumber. However it will require some space and additional power. Milling equipment also requires training and can be noisy. It is important to know the laws that govern your locality if you plan on using your mill.
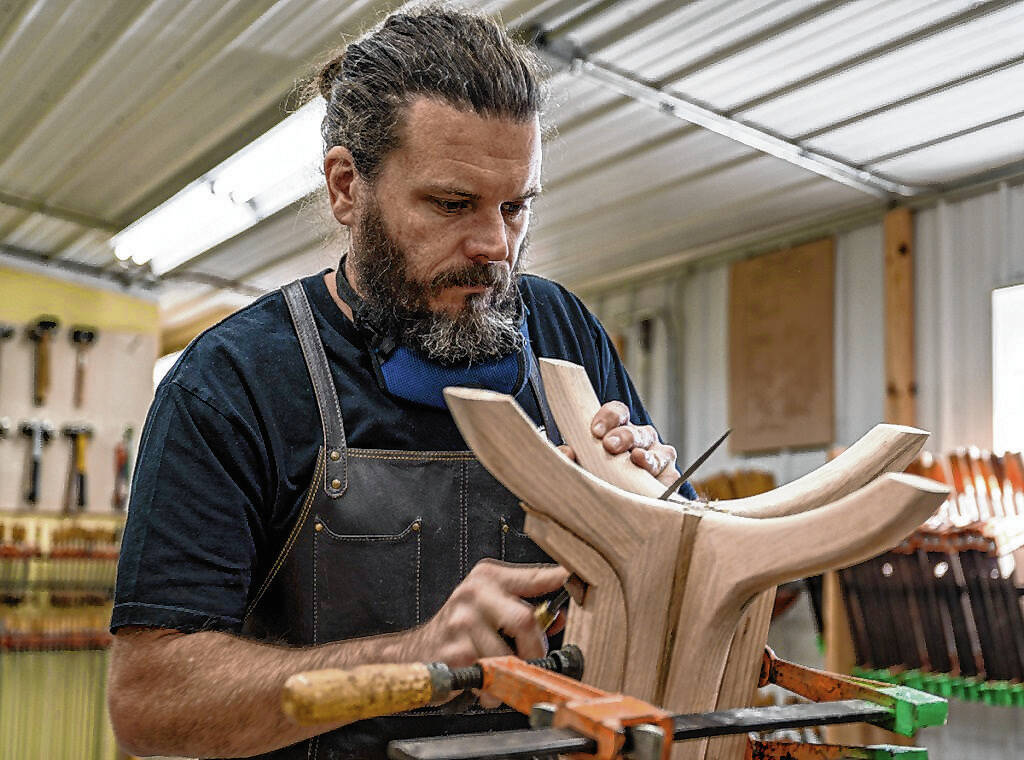
Source
There are many options available when you buy lumber. There are many different sizes, shapes or finishes that you can choose from. Rough sawn lumber, by example, is unfinished lumber. It has been cut into boards. This type of lumber tends to be stronger than other types because it carries extra moisture, but it is also thicker than surfaced wood. Here are some of the benefits you get from rough sawn lumber when woodworking.
The first benefit is its availability and low price. Rough lumber does not need to be treated and cannot usually be purchased at a hardware shop. However, this type lumber comes with its own pros and cons. This lumber is cheaper per board foot but less expensive by volume. Additionally, it takes longer to finish than treated lumber. This is why you might consider it when deciding on how much lumber you want to purchase. For projects that will require rough sawn lumber, you might want to purchase a large amount and some for finishing.
FAQ
What is the difference between plywood and particle board?
Plywood consists of layers made from wood and pressed together by pressure. Plywood comes with a range of thicknesses, and it is most commonly used for flooring and cabinets. Particle board is made of sawdust and resin that has been compressed into large blocks. It's commonly used for home improvement projects. Both types of boards are durable and easy to cut.
Can I make my living doing this job?
Yes! In fact, most woodworkers already have it. According to U.S. Bureau of Labor Statistics (BLS), woodworkers earned a median annual salary of $34,000 in May 2012. That's higher than the national average of $31,000 per year.
How can you calculate woodworking pricing?
It is essential to calculate costs as accurately as possible when pricing any project. It is important to ensure that you are getting the best materials prices. You should also consider other factors that could impact the cost of your project, such as experience, skill level, time, and money. If you want to get an idea of what you can expect to spend on different types of woodwork projects, check out our guide to the average price of common household DIY tasks.
How much do hobbyists need to invest in starting a business?
A lot of capital is required to purchase the necessary supplies and tools if you want to start your own woodworking shop. It's a good idea to buy a small tablesaw, drill press and circular saw. These items aren’t too expensive so you won’t have to break the bank.
What woods can be used to make furniture?
Woods are classified according to their hardness. Softwoods include pine, fir, cedar, and cypress. They're often used for outdoor furniture because they don't rot easily. You can find hardwoods like oak, maple, mahogany, teak, and others. Because they can't weather outside, they're usually used indoors.
Statistics
- Woodworkers on the lower end of that spectrum, the bottom 10% to be exact, make roughly $24,000 a year, while the top 10% makes $108,000. (zippia.com)
- The best-paid 10 percent make $76,000, while the lowest-paid 10 percent make $34,000. (zippia.com)
- Overall employment of woodworkers is projected to grow 8 percent from 2020 to 2030, about as fast as the average for all occupations. (bls.gov)
- Average lumber prices rose about 600 percent between April 2020 and May 2021. (familyhandyman.com)
External Links
How To
How to stain wood
The process of staining wood involves the application of chemicals to the wood's surface, which causes it to change its color. This chemical reaction causes the wood to change from white to brownish red. Oak is the most commonly used wood for staining, but other woods can also be stained.
There are several ways to apply stains to wood surfaces. Mixing the stain in a solvent such as turpentine and spraying it onto the wood is one method. Some methods involve a mixture of water and dye that is applied directly to the wood. The stain can be mixed with paints and varnishes to become part of the final coating.
The first step in staining wood is preparing the surface. The wood must be thoroughly cleaned to remove all grease and dirt. Sanding can smoothen out scratches and uneven spots. The next step is to choose the stain type you want. There are two types of stains that can be used: penetrating and non-penetrating. Penetrating stains penetrate deeper than non-penetrating stains, which makes them great for dark colors like mahogany. Penetrating stains are best paired with lighter colors, such as maple.
After you've decided what type of stain to apply, get ready for your tools. The best tool for applying stains is a paintbrush. It allows you to evenly distribute the liquid over the surface. After you're done painting, make sure to have some rags handy to remove any excess stain. If you are planning to mix your stain, ensure you have enough containers for each component.
After you have prepared your materials for staining, clean the area. Use soap and warm water to remove dust and grime. You can wipe down the entire furniture using a damp rag with clean water. Be sure to get rid of all loose material, especially if staining is planned for darker wood.
Apply the stain next. The stain can be applied by spraying or brushing the stain onto one end of the furniture. Slowly and carefully move along the grain of wood, slowly but steadily, until you reach the other end. Be careful not to let the stain drip off the wood's edge. Before you proceed with the next steps, let the stain dry completely.
Clear polyurethane is used to protect the painted surfaces. Three coats of polyurethane sealing agent are required. Allow the third coat, which should dry overnight, to dry before sanding.