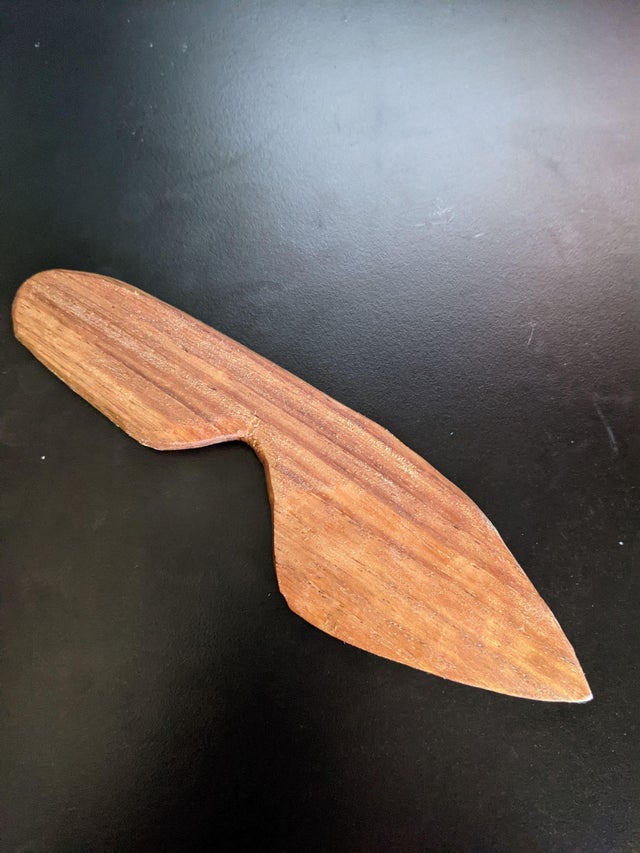
The ball in a cage carving is an intriguing one. At first, it might seem like a complex carving, but this simple piece only requires a single block of carving material. In fact, the two objects are intertwined. This article will discuss the methods and materials used in the carving as well as differences between later and earlier carvings. You can read on to learn about the different types used in cage carvings.
Techniques
To carve a ball in a cage, the first step is to cut the block and shape it. It should measure approximately 3 inches in diameter. Then, place pencil marks about one-half inch from both ends of the block. Continue to cut the block so that it slides smoothly along the rails. To round it, make small cuts at both ends. The rest of the wood can be cut with a handsaw. Be careful not to remove too many.
After you have cut the cube out, make a template of the shape you want. With a paper ruler, trace the squares onto the cube. Connect the squares' corners by using connecting line. You can also use a depth gauge to measure the distance from the template to the cutout. This distance will determine the depth and size of the inner-cage. The finished piece should measure approximately two-thirds of the original cube's height.
Materials
Ball in the cage carvings make for a very unique project. This piece of woodcarving may seem complicated at first but it is actually very easy to do. A single block of carving material is used to create the cage and ball, and they are both carved in a manner that leaves the two objects intertwined. The carving process is fun and easy. Soon, you will be carving attention-grabbing favorites!
To start carving your ball in a cage, you'll need to prepare a block of wood with an appropriate diameter and length. This block should be approximately 3 1/2" long by 3 1/2" wide. Next, measure the block length with a pencil. Leave a half inch gap at each end. When you're cutting the block, remember to scrape off the pencil marks. You can then create the desired shape by carving individual bars.
Comparisons
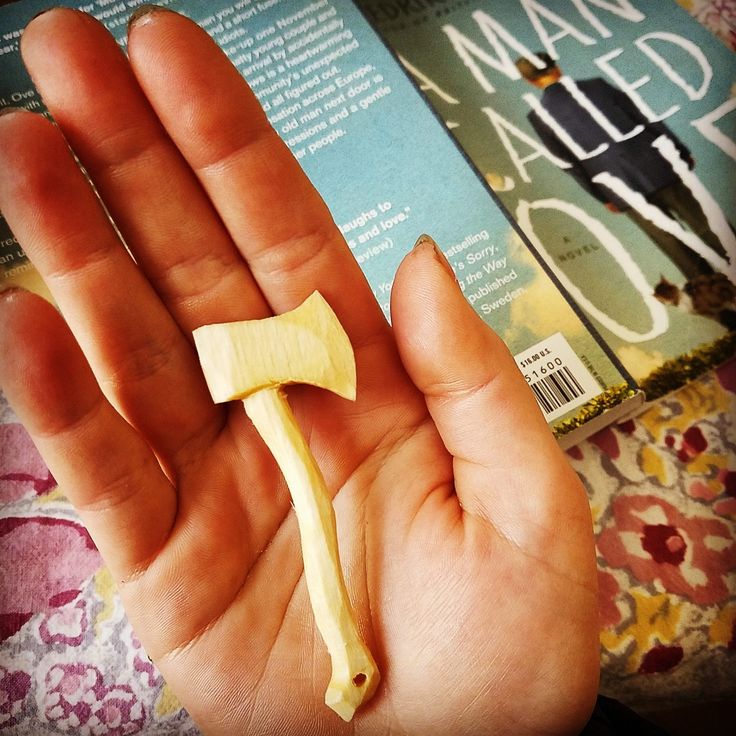
A ball in a cage is the perfect project for beginners in woodcarving. Not only is this project an excellent way to practice your new skills, but it is also a great gift idea for Valentine's Day or a birthday. A ball in an enclosed cage can be used for a drinking cup. Here are a few examples for carvings of a bird in a cage you can give to someone as a gift.
Later and early carvings
The iconic Civil War object was the ball in a cage. It was part a larger Civil War collection. Made of a single piece of wood, the ball in a cage measures approximately 4 1/2 inches in diameter. It could have been used to keep a soldier busy. These types of carvings were very popular in 1840s. But, over time, they have become less common. We will be looking at both early and later ball-in-a-cage carvings in this article.
It is rare to find balls with intricate carvings. They range in size between 2+3/4inches across with between 3 and 160 knobs. Some are completely unadorned, while others have intricate engravings. Some ball in a box carvings have knobs that can be adorned with multiple designs. One knob is shaped like a lion.
Sources
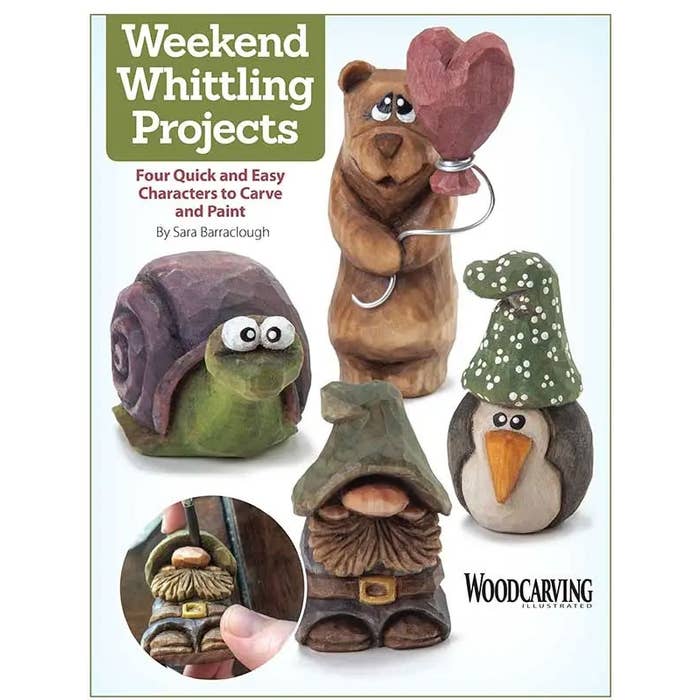
Jespersen explains how he makes his wood carvings, and how readers can make their own prototypes in his book "Carving a Ball in a Cage." He also discusses the tools and methods required to do this type of carving. He explains how to prepare a blank of wood and draw lines to guide his carve. He also explains how to carve cubotetrahedrons and dodecahedrons.
FAQ
What material would your recommendation be to learn woodworking?
You can start with softwoods like pine or poplar. You will feel more comfortable with these softwoods, so you can move onto hardwood.
Which wooden items are very popular?
Most wooden items that are best-sellers are made from wood harvested sustainably.
The most popular types of wood for furniture include oak, maple, cherry, mahogany, walnut, and teak.
These woods not only have great strength, but also beautiful patterns and colors. If they are well cared for, they can last many years.
To protect wood furniture from moisture damage, it should be painted first. This includes all surfaces, including drawers, doors, and handles.
Paint that is water-resistant will ensure furniture lasts for a long time.
A high-quality oil-based primer should be used, followed by two coats with top coat. It is possible to apply multiple coats depending on how heavy the wear.
You should avoid using aerosol paints or spray cans. These products contain solvents that evaporate quickly and leave behind harmful fumes.
How much should a woodworker charge per hour?
The hourly rate of a professional woodworker depends on many factors including experience, skill level, availability, location, etc.
The average hourly rate for a skilled woodworker ranges from $20-$50 an hour.
A less experienced woodworker may charge as little as $10 an hour.
Where can I begin with woodworking
Building furniture is the best way to learn how furniture is made. Although you will need to have tools and may make mistakes along your journey, you'll soon be able to master it.
Begin by choosing the project that you want to finish. It can be something as simple and small as a box, or large-scale as an entertainment center. Once you've settled on a project find a local skilled woodworker. Ask your local woodworker to help you determine the right tools for you and where they are located. You might even ask whether there's someone else you can talk to who does this kind of work.
Do you have any advice on how to start a woodworking business.
It's not easy to start your own woodworking business. However, if you are passionate about your hobby you will be willing to put in the effort. You'll likely enjoy the challenge of owning your business.
One thing to keep in mind when launching a new venture is that you might encounter unexpected problems along the way. You may run out of money suddenly. Maybe customers won't be willing to pay what you want. These situations are necessary for survival.
One good tip is to set up a separate bank account specifically for your business. You will always know how much money you have coming in.
What kind wood should I use for my project?
Oak, maple, cherry and mahogany are the most common wood types used for woodworking. Each type of wood has its own unique characteristics that can affect the final product's appearance. For example, oak tends to be darker and harder than other woods. Birch is soft and lightweight, while mahogany is denser and heavier. You can also choose from solid wood or veneers. Veneers can be described as thin sheets of wood that have been glued together in one layer.
How do I identify the type of wood that I am dealing with?
When purchasing wood, always check the label. It should have information about the wood species as well its moisture content and whether any preservatives were used.
Statistics
- Woodworkers on the lower end of that spectrum, the bottom 10% to be exact, make roughly $24,000 a year, while the top 10% makes $108,000. (zippia.com)
- Overall employment of woodworkers is projected to grow 8 percent from 2020 to 2030, about as fast as the average for all occupations. (bls.gov)
- The U.S. Bureau of Labor Statistics (BLS) estimates that the number of jobs for woodworkers will decline by 4% between 2019 and 2029. (indeed.com)
- The best-paid 10 percent make $76,000, while the lowest-paid 10 percent make $34,000. (zippia.com)
External Links
How To
How to make wood joint
This tutorial will show you how to join two pieces of wood together. We will be using the "pocket-hole joint", which involves drilling holes in wood and then gluing them together. This method is great if your wood's straight and smooth. If your wood isn't straight or flat, you might want to try another method, such as dowel joinery. Here are the steps
-
Drill Pocket Hole Joints. To start, measure and mark where you want to put the pocket hole joint. Use a jigsaw or handheld drilling machine to drill 3/8 inch deep holes at the ends of each wood piece.
-
Sand Smooth. Sanding the edges of the wood will help to prevent the joint from splitting later.
-
Glue Together Apply glue to the sides of both wood. Allow the wood to rest for five minutes before clamping it together.
-
Connect the pieces. Once the glue has dried, clamp the pieces together so they are flush.
-
Trim Joinery. Trim the excess wood around the joint after the glue has dried completely.
To be able to turn the pieces inside-out, leave enough room between them.