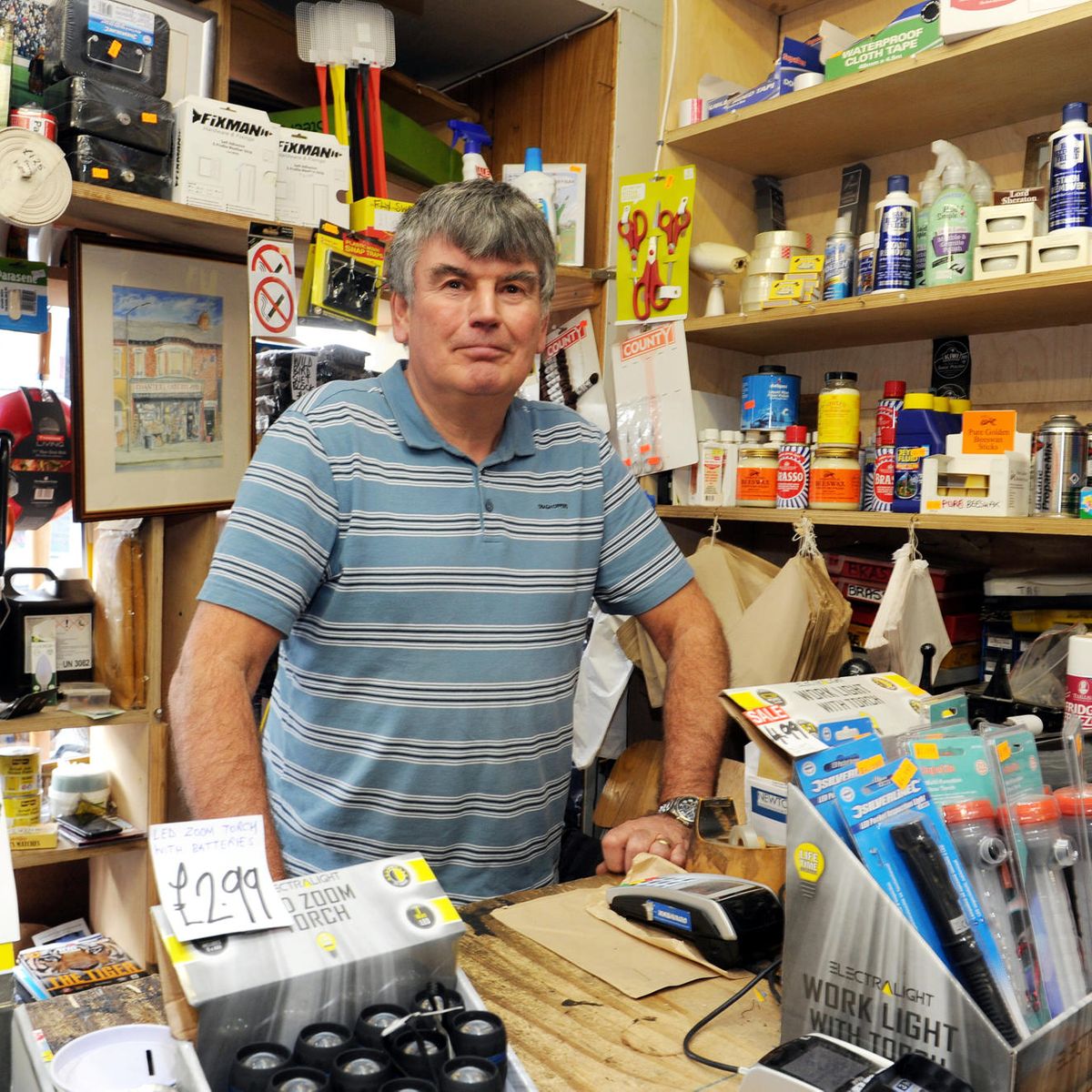
It can be challenging to transport rough lumber by hand. Bring your tape measure, hand saw and saw to the hardware store. Additional boards can be purchased in case the one you have bought doesn't fit. Make sure you have the right knots and checks on your board. Otherwise, they might not fit as well as you would like. You don’t want to have the board ripped and re-made. This is a wasteful way to spend your time and money.
Less wastage
A sawmill usually turns 59% of rough lumber into boards when cutting it. The remainder of the log can be considered waste, including sawdust, bark, chips and chips. A less-than-perfect cut results in more waste, but it should still be less than 20%. Here is a simple formula that will estimate how much wood has been wasted in a given board. For a nominal 4-foot board, the sawmill should remove about 18% of its volume to achieve the desired lumber thickness and width.
For one, rough lumber is rarely available in uniform dimensions. The dimensions of hardwood that you purchase from a big box retailer are often known. This allows for you to plan your project using the standard size. It is possible for rough lumber to have uneven edges, leading to waste. A lot of lumber is wasted because rough-cut lumber requires a standard width. Furthermore, this waste can't ever be reused.
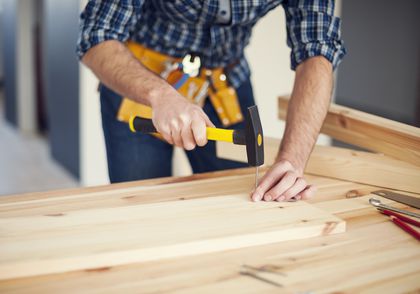
Preparation
Measure the length of your material before you start cutting rough lumber. The lumber yard may not have the rough lumber perfectly flat upon arrival. You may need to flatten it several times as it may not have parallel edges or faces. As a rule of thumb, you should remove 1/16 inch per pass. If the lumber has concave surfaces, run it through the saw with the concave surface down.
Rough cut lumber should be flattened to a thickness of 1/4 inch before it is cut. After flattening the surface, plane to the final thickness of the board. Once you have the thickness of the rough lumber, measure the finished width and length. You should account for any imperfections. Plan your project around the boards available. You will have a difficult time working with rough lumber if it is warped, bent, or twisted.
Cost
There are two types if lumber: rough-sawn lumber and dimensional lumber. Home improvement stores generally carry finished lumber but very rarely rough-sawn. Both types of lumber can be found in local lumber yards and sawmills. There is a difference in how much work it takes to process the two types. The cost of rough-sawn lumber is lower because it needs less processing. It is also smaller and lighter than finished lumber.
While buying lumber from a yard or mill is cheaper, you are less likely than others to find it in standard lengths. Although milling your own lumber is cheaper than buying rough-sawn lumber it can still be an economical option. However, you will need to have enough shop space and more power. Milling equipment can be noisy and requires training. You might want to check the zoning laws for your area before you start using your mill.
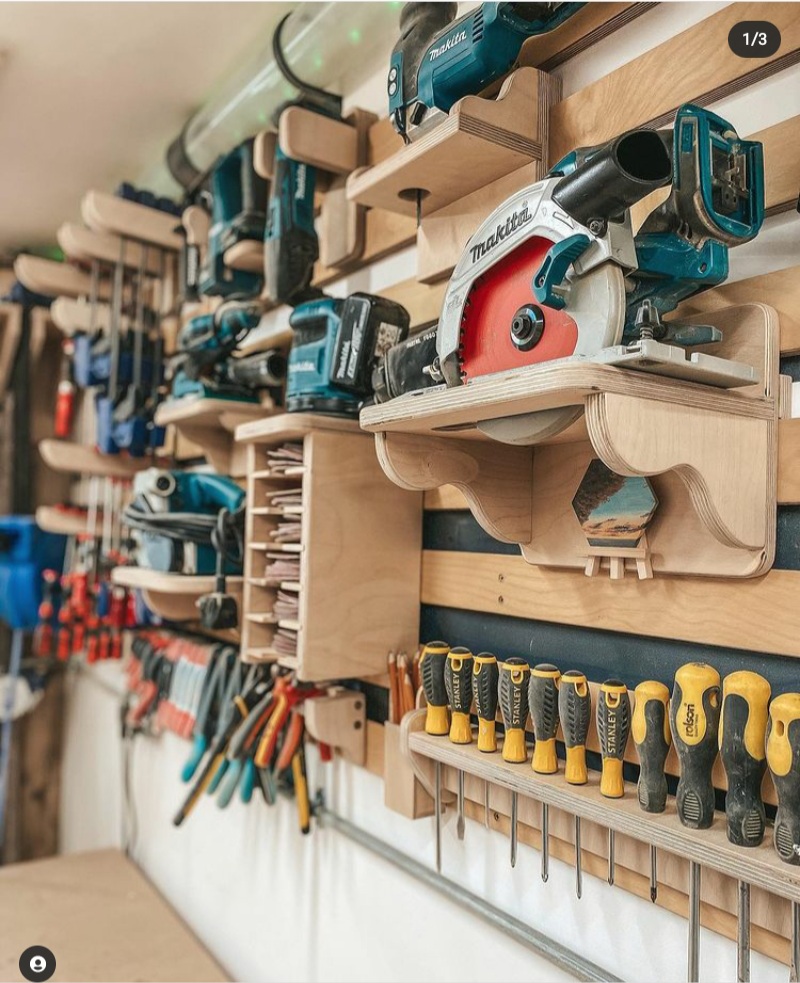
Source
There are many options for lumber purchases. There are different sizes, shapes, cuts, and finishes to choose from. Rough sawn lumber for example is unfinished lumber that has not been sanded or finished and which has been cut into planks. This lumber tends be more sturdy than other types, as it has more moisture. Additionally, it is thicker that surfaced wood. The following are some benefits of using rough sawn lumber for your woodworking projects.
The first pro is its low cost and availability. Rough lumber is not treated and is not usually sold at a hardware store. But, rough lumber has its benefits and drawbacks. It's cheaper by volume but more expensive per board foot to haul. Also, this wood is more labor-intensive than treated wood. When deciding how many lumber to buy, this is an option you may want to consider. Consider purchasing large quantities of rough sawn lumber and small amounts for finishing if you intend to use it for your project.
FAQ
Are you a genius in order to master woodworking?
No. It is not rocket science to woodwork. To create stunning works of art, anyone can learn to use basic power tools.
Is it possible to learn woodworking by yourself?
You can learn everything best by doing. Woodworking requires patience, practice and skill. Any craft requires patience to master.
It is the best way to learn to do something is to actually do it. Start small, and work your way up from there.
How do I know what type of wood I'm dealing with?
Always verify the label on wood purchases. The label should contain information about the wood species, its moisture content, and whether it has been treated with preservatives.
Statistics
- If your lumber isn't as dry as you would like when you purchase it (over 22% in Glen Huey's opinion…probably over 10-15% in my opinion), then it's a good idea to let it acclimate to your workshop for a couple of weeks. (woodandshop.com)
- Most woodworkers agree that lumber moisture needs to be under 10% for building furniture. (woodandshop.com)
- In 2014, there were just over 237,000 jobs for all woodworkers, with other wood product manufacturing employing 23 percent; wood kitchen cabinets and countertop manufacturing employing 21 percent. (theartcareerproject.com)
- The U.S. Bureau of Labor Statistics (BLS) estimates that the number of jobs for woodworkers will decline by 4% between 2019 and 2029. (indeed.com)
External Links
How To
How to stain wood
The process of staining wood involves the application of chemicals to the wood's surface, which causes it to change its color. The wood will turn from white to brownish-red due to the chemical reaction. Oak is the most common wood type for staining. However, you can also use other wood types.
There are many ways to stain wood surfaces. Some methods include mixing the stain along with a solvent like turpentine and then applying the mixture to the wood by brushing or spraying. Others use a solution made up of water and dye, which is then applied directly onto the wood. The stain can be mixed with paints and varnishes to become part of the final coating.
The first step in staining wood is preparing the surface. To apply the stain, clean the wood completely. Sanding smoothens any scratches or rough spots. Next, you need to decide which stain you want. There are two types of stains that can be used: penetrating and non-penetrating. Penetrating stains penetrate deeper into the wood than non-penetrating ones, making them ideal for dark colors such as mahogany. The best non-penetrating colors are those that work with light colors like maple.
After deciding on the type of stain, you want to apply, prepare your tools. You can use a paintbrush to apply stains. This allows you spread the liquid evenly over the surface. After you're done painting, make sure to have some rags handy to remove any excess stain. If you intend to mix the stain yourself you will need enough containers to hold all the components.
After you have prepared your materials for staining, clean the area. You can remove grime and dirt with warm water and soap. Use a dampened sponge and warm water to clean the entire piece. If you intend to stain darker wood, make sure you get rid of any debris.
Next, apply the stain. Apply the stain by brushing or spraying it onto one side of the furniture. Slowly and carefully work your way along the grain to reach the opposite end. Keep the stain from dripping off the wood's surface. Allow the stain to dry completely before you move on to the next step.
To protect the painted surface, apply a coat of clear polyurethane sealant. Three coats are recommended for polyurethane. Allow the third coat to dry overnight, before sanding.