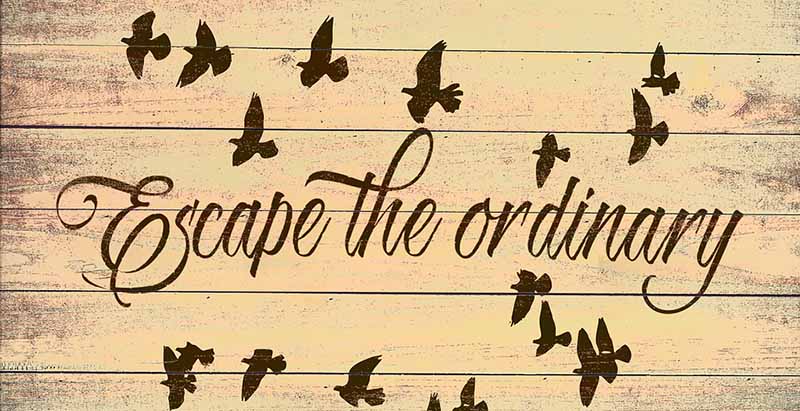
You might be interested in learning about pyrography on Cedar if you are interested in creating unique pieces for your home. This ancient art involves burning intricate decorations and designs into wood. It dates back at least to the 17th-century. The result is beautiful burn marks that create dark designs. These can include landscapes or portraits. This technique has been around for centuries, and is a popular choice for home decor.
Yoko sugi ban
In Japan's 18th century, shou sugiban is a method that preserves wood by charring its surfaces. This creates a rich charcoal-black color on the wood's exterior, which can also give it an Alligator skin or cracked appearance. Japanese cedar is most commonly used for its rustic appearance. However, other wood types may also be used with varying degrees. This controlled charring process is a great preservation technique that strengthens the wood and prevents future damage.
Shau sugi ban
The method of removing char is the most noticeable difference between traditional sanding and shou-sugi ban. Some woodworkers using shou-sugi ban use wire brushes to remove the charred top layer, while others use coarser sandpaper. Either way, you need to scrape enough char away to reveal the brownish-black color underneath. You will see a pattern that resembles an alligator skin. To remove excess char, sanding is required.
Shau sugi ban on cedar
The shou sugugi ban of pyrography gives wood a lovely finish. However, this ban has practical implications. It is possible to track bits of charred lumber throughout a building. They can also be inhaled and inhaled from people who are inside the treated area. To combat this problem, pyrographers are beginning to use propane torch in addition to the traditional wood-burning method. Let's take a look at some of the differences between these two styles.
Yaki Sugi Ban on Basswood
The centuries-old Japanese technique of yakisugi ban (on cedar) can give wood beauty and strength. Although sometimes called Shou-sugi ban, the process involves charring wood to create beautiful patterns. It is so common in Japan, cedar is used for many shou-sugi ban projects. Satoshi Yamamura, the operations director of a Japanese wooden company, explains why shou Sugi Ban is so popular and what this means for woodworkers.
Yaki sugi ban on blue stain pine
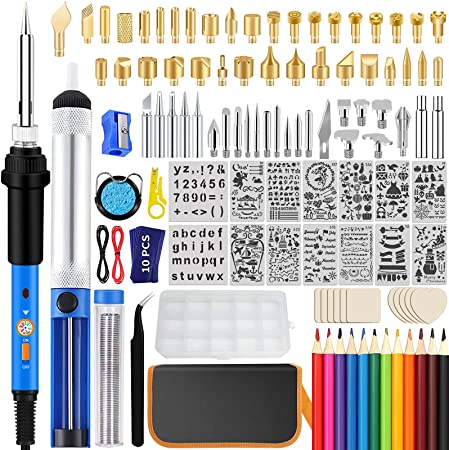
This is commonly known as shou-sugi ban. It preserves wood using fire. Traditionally, cedar was used in shou sugi banning, but other types are acceptable. Even though cedar is the most traditional wood for this purpose, yakisugi can also be used with maple, ash or birch. This technique is popular among traditional Japanese craftspeople.
Shau sugi ban on basswood
Charring cedar creates a deep black, rich color and crackled surface. Cedar is naturally water-resistant and repels pests. However, the charred surface has sculpting qualities. The two types of charred timber are untreated or reclaimed. You can also treat a cedar panel to create a subtle burnt wood look.
Shau sugi ban on jelutong
Shou sugi ban on wood pyrography has many benefits. The technique improves wood's natural patterns. Because of the thicker carbon layers, charred timber is more durable. It all depends on the wood species used and the environment it is placed in. Shou sugi ba is an environmentally friendly method to treat wood.
FAQ
How much money will I need to get started?
Since every project differs, it is impossible to give exact numbers. These factors will help you get an estimate of how much money is needed.
-
Cost of materials
-
Tools and equipment
-
The time spent on the project
-
The hourly rate
-
How much profit do you expect to earn
-
No matter if you are looking to hire someone
Start small, if possible. You can make simple boxes or picture frames if you're just getting started. As you gain experience, more difficult projects will become possible.
Do I have to refinish my furniture?
Yes! You don't have to hire a professional to refinish furniture. There are many ways you can do it yourself. Here are a few ideas:
To remove stains and scratches, use sandpaper. Then wipe down the surface with a clean cloth.
Apply clear polyurethane finish. Allow to dry thoroughly before moving furniture.
Paint furniture with acrylic paint.
Instead of painting, use stain. The furniture will have a rich look thanks to the stain.
Shellac wax can be applied. Applying wax will give the wood shine and protection.
Are you able to teach yourself woodworking
Doing is the best way to learn any subject. Woodworking is an art form that requires patience, practice, skill, and experience. Mastering any craft takes time.
It is the best way to learn to do something is to actually do it. Start small and learn from your mistakes.
Can I make my living doing this job?
Yes! Many woodworkers have this ability. According to the U.S. Bureau of Labor Statistics in May 2012, the median annual income for woodworkers was $34,000 That's higher than the national average of $31,000 per year.
How much should a hobbyist invest to get started?
You will need capital to purchase the tools and supplies you need to start your woodworking business. You can start by purchasing a small table saw and drill press as well as a circular saw, circular saw, jigsaw and sanding machines. These items are affordable so you won’t break the bank.
Statistics
- Most woodworkers agree that lumber moisture needs to be under 10% for building furniture. (woodandshop.com)
- Average lumber prices rose about 600 percent between April 2020 and May 2021. (familyhandyman.com)
- The U.S. Bureau of Labor Statistics (BLS) estimates that the number of jobs for woodworkers will decline by 4% between 2019 and 2029. (indeed.com)
- Overall employment of woodworkers is projected to grow 8 percent from 2020 to 2030, about as fast as the average for all occupations. (bls.gov)
External Links
How To
How to make wood joints
This tutorial will show how to join 2 pieces of wood together. The "pocket hole joint" is a method whereby we drill holes into the wood and glue them together. This method works great if your wood is straight and smooth. If your wood isn't straight or flat, you might want to try another method, such as dowel joinery. Here are the steps
-
Drill Pocket Hole Joints. You will need to measure and mark the exact location of your pocket hole joint. You will then drill 3/4" deep holes through each piece of wood with a jigsaw, handheld drilling machine, or hand-held drill.
-
Sand Smooth. You can sand the edges of the wood to ensure that it doesn't split.
-
Glue Together Apply glue to both ends of the wood. Allow it to cool for at least 5 minutes before you attach the pieces.
-
Attach the Pieces together. After the glue has dried completely, you can clamp the pieces together until they are flush.
-
Trim Joinery. Trimming the joinery after glue has completely dried.
You should leave enough space between the pieces to allow you to turn them inside-out.